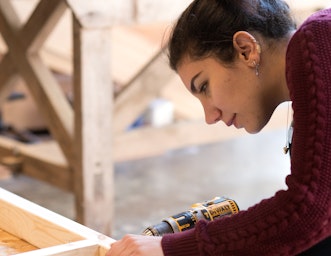
Windows
Replacement glazing will be one of the most expensive parts of a renovation, so making good choices is important. Your choice will also affect the environmental impact, lifetime and maintenance needs of your new windows. Fitting secondary glazing inside old windows will sometimes be more suitable than replacing windows.
In CAT’s Zero Carbon Britain report, we target a 50% reduction in heating demand. Improving windows and other glazing is a big part of this. One-fifth of the heat lost from a home can be due to old single-glazed windows. Modern double-glazing should be three times better, with triple glazing five times better.
Double or triple glazing?
When building or renovating to a very high standard – such as ‘passivhaus’ – you’ll be looking at triple glazing. For many renovation projects double glazing may be fine – perhaps fitted as secondary glazing. You want to allocate your budget carefully and get a good balance of insulation measures across the whole house. The extra weight and thickness of having a third pane may be an issue in some renovation projects.
It’s important for the installation of windows to be done well. If the airtightness around the frame is poor, a high-performance window can be badly compromised.
Specifications
Double glazing panes with a low-E (“low emissivity”) coating and an argon gas fill are now common. You’ll need windows with these measures in order to meet the minimum current building regulation standards.
Low-E coating is a very thin layer of metal on the outer surface of the inner pane. This coating reduces heat transfer across the gap. Argon gas does not conduct heat as well as air. Therefore, putting argon gas in the gap between the panes improves the performance of a window. Krypton gas fill will lead to even less heat loss than argon gas, but it is lot more expensive. You may only need krypton windows if a very thin profile is needed to meet conservation glazing standards.
The gap between the two panes of glass should usually be about 20mm – a very narrow gap tends to gives a slightly worse performance. A bigger gap won’t make much difference, except that it can give better sound insulation. Windows with lots of glazing bars (Georgian style) don’t perform as well – the multiple bars conduct heat out.
Comparing performance
U-values measure thermal performance, and a lower U-value means less heat loss. Overall energy savings will depend on the house design, the number of windows, orientation, location, and so on. When renovating to a high standard, the u-value of each choice can be entered into design software. The difference in performance can then be modelled and compared.
Specification | U-value |
Single glazing | 5.5 |
Standard double glazing | 2.7 |
Double glazing, low-E coating | 1.8 |
Double glazing, low-E coating and argon-filled | 1.6 to 1.3 |
Triple glazing, multiple low-E coating and argon-filled | less than 1.0 |
Wood, metal or PVC Frames?
We recommend good quality timber frames. These use less energy in manufacturing, can last for over 50 years, and can then be renovated rather than replaced.
In contrast, uPVC window frames require more energy to manufacture and lead to higher pollution problems at manufacture and disposal. Aluminium manufacture involves a lot of energy use and pollution and some frame coatings make recycling difficult. This is not ideal for such a high-value material, so if you have to use aluminium, look for anodized frames.
Wooden frames had a poor image in the past, as UK-made softwood windows were often of low quality. However, we’ve learned from the Scandinavians and it’s possible to get UK-made windows with high standards of airtightness, built from homegrown, durable, untreated wood.
Which wood?
Our first choice is FSC-certified temperate (not tropical) hardwood or durable softwood. A durable temperate hardwood like oak, sweet chestnut, or larch (softwood, but durable) won’t need treating and should last 30 years. Other durable softwoods include Douglas Fir and European Redwood.
Window frames should be made with heartwood – as this is the most durable and resistant to movement. To resist twisting, some windows frames use engineered wood. This is layered and glued sections of wood (like plywood or glulam).
The preservatives used to protect less durable softwood will cause pollution at the eventual disposal. If you choose a less durable wood, look for one pre-treated with a low-impact natural, renewable treatment. Any sustainable timber is preferable to uPVC, but painting wood does increase the environmental impact.
Secondary Glazing
If you’re on a tight budget, you can improve the performance of old windows instead of replacing them. A simple and cheap alternative is to add some form of secondary glazing, as well as thick well-fitting curtains. The best quality secondary glazing will be an extra window, but a rigid pane or even just plastic film could work well.
The most advanced type of secondary glazing is to fit a new second window inside the existing one. This will often be cheaper than replacing windows altogether, especially where more restrictive planning rules apply. You could hire a local joiner to make them, or look for an off-the-shelf system in a DIY store.
Rigid (or slightly flexible) plastic sheets are also usually available from DIY outlets. Panes that are held in place magnetically are easier to clean. More advanced options could be a single pane in an aluminium frame attached on hinges or sliding runners, or perhaps an old window cleaned up and fitted inside the frame. There are also specialist films that improve the performance of glass by letting through certain wavelengths of light in only one direction.
Clear plastic film (polythene) should be available from DIY stores. You attach it to the interior frame around the edge with double-sided sticky tape. Then you heat it – which first makes it stretch but then it contracts as it cools and clears any wrinkles. It won’t last a huge length of time – probably one winter – but is very cheap.
Planning and building control
Replacing either glass units (e.g. broken windows or faulty double-glazed units) or some rotten wood in the frame or sash should not need Building Control approval. When replacing an entire window frame and the opening parts of a window, or a door that is more than 50% glazed, you will need approval. By employing a FENSA registered (Fenestration Self Assessment) joiner or installer you won’t need to get the work checked. Instead, the installer issues a certificate to verify compliance with Part L of the Building Regulations.
For properties such as listed buildings the requirements can be strict, but high specification windows or secondary glazing are available. ‘Conservation grade’ replacements replicate the appearance of old windows but have much greater levels of insulation and air-tightness. For more advice on the sympathetic replacement or upgrading of windows in old buildings, see these free guides from Historic England.
Funding and Support
To find any local grants available in the UK for energy-related measures, check with your local authority. See also the Government’s Help to Heat summary page. In Scotland or Northern Ireland try either Home Energy Scotland or NI Energy Advice.
Further information
We offer many short courses at CAT, including our long-running eco-refurbishment course. See also this blog post about eco-refurbishments by our course tutor, Nick Parsons.
The BFRC energy label for windows gives an overall assessment of performance, so can be a help when choosing windows. There’s also useful further reading on the Greenspec website. Information about conventional windows and prices is available from the Energy Saving Trust.
Related Questions
What is breathability?This can be a confusing term for two reasons. Firstly because it refers to moisture not air and secondly because the exact physical processes which go on in a building are complicated (and still being researched). However the metaphor of breathing captures the important idea of continual movement. Moisture in itself might not matter, as long as it doesn’t take up permanent residence in your walls.
Broadly, breathability is the ability to buffer moisture – to soak it up and then release it – thus avoiding a situation where water vapour is retained by the fabric of a building. The technical term for this property is hygroscopic. Natural materials tend to be more hygroscopic than synthetic ones. The term “vapour permeable” also gets used in this context, referring to materials that allow water vapour to pass through at a certain rate.
A breathable construction will be made up of a gradation of vapour permeable materials, with the materials towards the inside being less vapour permeable than the materials towards the outside. A rule of thumb is that the material on the inside (warm side) should have five times the vapour resistance of the material on the outside (cold side). Without using a very high resistance material such as polyethylene or foil-backed board, this can be achieved with a suitable vapour-check layer on the warm side of the insulation. This layer slows down the passage of moisture to a safe level.
The construction also needs to be airtight on the inside to ensure the vapour-check layer works as intended. So it’s important to not put gaps in the vapour check layer for services (wires, etc), and instead have a thin space for these services between the vapour check and the internal finish (e.g. plasterboard). The final layer of external cladding might be waterproof (such as tiles) but there must be a ventilated gap between this and the sheathing board that actually completes the breathable construction.
In a UK-type climate the interior of a house usually has a higher relative humidity (RH) than the outside because it contains people exhaling, cooking, and washing. It’s a very general rule that, left to themselves, things will always migrate from an area of higher concentration to one of lower concentration, so there will be movement of water vapour towards the outside (or, to be more technical, the interior has a higher vapour pressure).
At times of high interior RH, water vapour will enter the walls, lowering the RH (both high and low RH cause problems and the ideal range is 40-60%). At times of lower interior RH, almost all of the water vapour will migrate back into the interior to be taken away by air currents. Any water vapour that might have managed to penetrate the wall deeply will be drawn out towards the exterior because of the lower permeability of the outer layers, so no harm done. Any water coming in from the outside will be unable to get very far as it is pushing through layers of decreasing permeability. The breathability of materials interacts with both temperature (which affects RH) and ventilation (one of whose functions is to carry away water vapour).
There are basically three different types of insulation material:
- Organic – those derived from natural vegetation or similar renewable sources, which tend to require a low energy use in manufacture (a low ‘embodied energy’). Examples are sheep’s wool, cellulose, cork, wood fibre, and hemp.
- Inorganic – derived from naturally occurring minerals which are non-renewable but plentiful at source. Likely to have a higher embodied energy than organic materials. Examples are mineral/glass fibre, perlite and vermiculite (from volcanic rock) and rigid foamed glass.
- Fossil organic – derived by chemical processes from fossilised vegetation (oil) – a finite resource. Fossil organic insulation materials such as expanded polystyrene and polyisocyanurate or phenolic foam are highly processed, resulting in a high embodied energy.
Which is best?
If possible it is better to choose insulation materials that have not been heavily processed as this will reduce the carbon footprint and environmental impact of your home. But it is far better to install cheaper inorganic or fossil organic materials with the right physical properties and a low thermal conductivity than to install nothing at all.
In many cases, organic insulation material can be applied instead of inorganic or fossil organic, but there are exceptions. For example, there is not an organic insulation material suitable for cavity wall insulation.
Think also about the ease of installation. Loose fill insulation is quick to put in in lofts, but cannot be DIY installed in anything other than a flat place. Rigid boards and batts will come in certain sizes, but need to be cut to shape if you have some unusual spaces. Some materials can be cut with a knife, but a few will need a saw. Some mineral wool now comes in a thin foil or plastic wrap, to protect from the fibres. You should still wear a face mask when installing any type of installation, as small fibres of any kind are best not inhaled.
The first two of the following four methods involve adding insulation to the outside of the roof, so will be suitable if there is little headroom underneath, or if access is difficult. The second two involve adding insulation underneath the roof. If insulating on top of a flat roof, make sure that it still drains well so that water does not pool on top.
Upside Down or Inverted Roof
An ‘upside down’ roof uses waterproof insulation on the outside of the building structure. The insulation is laid over the existing waterproof membrane and held down with something – which could be pebbles, turf (for a green roof), paving slabs, etc. Suitable insulation materials will tend to be a bit more expensive, and include cork, foamed glass and closed-cell plastic foam. You’ll need to check that the structure can bear the weight of the insulation and finish. This option keeps the existing membrane, but there is a risk that water will percolate through the insulation and so cool down the roof deck – causing condensation.
Warm Roof
A warm roof will have the insulation laid over a vapour control layer (itself over the roof deck), with a membrane laid over the insulation and suitable finish on top. You’ll need to check that the structure can bear the weight of the insulation and finish. If you are replacing the roof membrane anyway, then this will be a better solution than the ‘upside down’ roof (above), as it will keep water above the insulation and so keep the roof decking warm. You could still keep the existing membrane underneath the insulation if it would be difficult to remove.
Cold Roof
The insulation is put between the roof joists. A ventilated gap needs to be retained between the top of the insulation and the roof decking, to avoid condensation build-up. It can be difficult to get adequate ventilation, so this method is often not recommended.
Internal Insulation
A method similar to dry-lining of walls can be used, with a plasterboard/insulation board added to the underside of the internal roof, below the joists.
A ‘cold loft’ roof, with the insulation at ceiling level (laid flat in the floor of the loft) is generally the most economical, and easy to install. However, if you want to insulate in the slope of a roof in order to make use of the space, then here are some tips.
The most economical way of achieving a good thickness of insulation in the roof slope is to have two layers of timber, one supporting the roof finish and another supporting the insulation and ceiling finish. Batts or loose fill insulation is generally better between rafters, because it will give a tight fit. Otherwise rigid material has to be very precisely cut to fit well.
To reduce cold-bridging, timber I-Beams or I-Joists can be used when adding new beams or building a new home.
In an existing roof (with rafters supported on roof beams), the second layer of timbers (ceiling joists) can be hung off the rafters using hardboard, ply or timber ‘hangers’, or nailed crosswise to them, or they can span between the roof beams. This technique can also be used with flat roofs.
An air space of 50mm must be left between the insulation and the tiling felt, unless the felt is of a low-vapour resistance type. If using a breathable membrane, with insulation up against it, then above the membrane you would put counter battens (top to bottom) as well as the standard battens (side to side), for adequate ventilation beneath the tiles. Sometimes, a breathable membrane is used with only standard battens, with the membrane slightly draped between rafters to allow ventilation – in this case an air gap of about 25 mm would be needed between membrane and insulation.
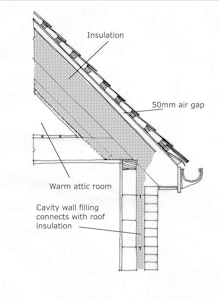
Thin wood-fibre boards (22 or 35mm thick) can be used as an alternative to a membrane under tiles. When re-roofing, the fibre-board is laid over the rafters, and then counter battens (in line with rafters), and then standard battens to fix the tiles/slates to. Thicker wood fibre boards can also be used, to give more insulation and achieve a lower U-value (to minimise heat loss).
A ‘warm roof’ will have waterproof insulation on the outside of the structure (so the main timbers are on the warm side of the insulation). It’s a useful way of upgrading an existing roof when internal room height is at a premium. On a sloping roof, the tiling battens are supported by rigid insulation and fixed through to the rafters by special screwnail fixings. The insulation must be waterproof, such as cork, foamed glass or closed-cell plastic foam board – these will tend to be more expensive than the standard insulation materials for internal use.
You can also read more at the webpage of the Energy Saving Trust, on Greenspec’s pages about ventilated and unventilated roof insulation options, and in a guide from Historic England.
Traditionally, solid floors were laid directly onto soil. This relies on the ground underneath being kept dry, usually by it being higher than the ground outside the building, and by having adequate drainage.
The most common method now used is to have a thick concrete slab laid on a damp-proof course (e.g. a polythene membrane). A layer of polystyrene insulation is then finished with sand/cement screed and tiles or board.
For a low-impact alternative to the above you could look into using recycled aggregate in the concrete (rather then newly quarried material), and perhaps using stabilised earth as the screed. You could also consider using recycled polythene or bitumen for the damp-proof course.
A solid floor of stabilised earth or limecrete should have a solid insulation material below it, such as cork, perlite or foamed glass, with recycled polythene vapour check and damp-proof membrane (DPM) below this.
Try to achieve at least 150mm of insulation for a solid floor. Insulation should be placed around the edge of the floor, and the floor finish supported on some sort of rigid insulation. Possible materials include cork, perlite (volcanic glass), lightweight expanded clay aggregate (‘Leca’), foamed glass (slabs or granules), fibreboard, mineral wool boards, or plastic foam of some sort. A vapour check layer will normally be required to prevent condensation occurring within the insulation layer.
Another possibility is a hemp & lime (or ‘hempcrete’) floor. Lime has a much lower environmental impact than cement, so if you can use it place of cement in mortars or concrete you will be reducing the ’embodied energy’ of the floor and the carbon emissions from construction. The hemp provides the insulation. See for example the details of how we insulated the WISE building at CAT.
If you are redoing a floor, then you may have the chance to consider underfloor heating. Because it runs at a much lower temperature than standard radiators, wet underfloor heating is more efficient and provides a more comfortable type of heat. It’s particularly appropriate for use with heat pumps, as these need to supply low-temperature water to run efficiently.
You can also see some information and examples on the Energy Saving Trust and Historic England websites.
If you can access the floor from below via an unheated cellar or basement it will be easier, otherwise you’ll have to lift the floorboards (which requires care to avoid damaging them).
225mm of a renewable or mineral fibre type of insulation is a decent amount. Make sure you keep good ventilation to the underfloor space beneath the insulation – with vents at either side for air flow.
Batts or loose fill insulation is generally better between joists because it will give a tight fit. Otherwise rigid material has to be very precisely cut to fit well.
Renewable insulation will need to be protected by a breathable membrane to protect it – if the floorboards are not well sealed. See the website of the supplier of insulation you’re using (or call their advice line) for advice on the type of membrane that would be needed. Natural insulation materials include hemp, sheeps wool, recycled textiles, recycled paper (loose fill), and wood fibre.
Loose fill insulation can be carried between the joists on a membrane or netting nailed to floor joists or on a low-vapour resistance board (for example softboard, a fibreboard bonded by heat rather than glues – this is good for Warmcel insulation made from recycled newspaper).
For other insulation materials (e.g. standard mineral fibre types) it will be worth looking on the website of the manufacturer as they’ll usually have guidance sheets on how the material should be installed and what limitations there may be.
You can also see some information and examples on the Energy Saving Trust and Historic England websites.
Condensation is due to excessive moisture, cold conditions, cold surfaces or inadequate ventilation. It can cause mould, heat loss and building damage. To address these issues, the room should be properly insulated and adequately heated (to keep the surfaces warm).
So do take all feasible insulation and draught-proofing options, and look into improving single glazing with either replacement glazing or with secondary glazing (a cheaper option).
Condensation may still occur on replacement windows, as they’ll still be the coolest surface. New windows will be more airtight than old ones, so warm moist air will be no longer be escaping through cracks in the frame and around the seals. This means that existing damp issues may become more pronounced. Many windows will include trickle vents in the frame, to allow a small amount of ventilation, but to keep the house warm and dry you may need to take a few other measures to avoid producing lots of moist air.
Drying clothes indoors can easily cause problems of damp and condensation, leading perhaps to mould, etc. So if you need to dry indoors, it should be in a room that can be shut off and ventilated (perhaps with heat recovery, as mentioned below).
The bathroom and kitchen in particular should be able to be ventilated in a controllable way, to stop moist air circulating into the rest of the house. For example, after a shower or bath, leave the bathroom door shut and the window open for a while until moist air & condensation on the window/mirror has cleared. Do the same when cooking if you can; if your home has an open plan layout at least stop the moist air circulation where possible (e.g. to the upstairs rooms).
To avoid heat loss from a room like a kitchen or bathroom, where lots of moist air is regularly produced, you could consider a heat recovery extractor fan. It may be worth getting a slightly bigger heat-recovery fan unit than you need, as they can be a bit noisy if they are operating on full power. This may be fine if are just switching it on for a short while to clear the bathroom, but it could be obtrusive in the kitchen. If a fan unit is not supplied with more solid covers over the plastic slatting, it could be worth fitting something if you live in a house that is a bit exposed to the wind (as they could let in draughts when not in use). An openable wooden casing could be fitted quite easily.
If drying clothes indoors is not an issue, and you’re already careful about venting away moisture from bathroom & kitchen, then excessive condensation may be from some other cause, such as a water leak somewhere (e.g. from a pipe under the floor or in the loft), or water penetrating the structure from outside (such as rainwater coming in cracks in masonry, or if gutters are broken). If problems persist, it would be worth investigating these issues, as over time they’ll cause damage to the building.
The U-value is a measure of how many watts (representing the rate of flow of energy) pass through one square metre (m²) of a construction detail (such as a wall) for every degree difference in temperature between the inside and the outside. Temperature is measured in kelvin, and 1K = 1°C (degree centigrade).
As an example, a U-value of 6.0W/m²K for a single glazed window means that six watts will be escaping through each square metre of glass when the temperature difference is one degree. If it is 20°C in the house and 0°C outside, then the heat loss is 20 x 6 = 120 watts per square metre.
U-values are generally used to describe the thermal performance (heat loss) for a section of construction that involves several materials – such as a wall made up of timber, insulation, board & render.
Thermal conductivity
For individual materials, such as a type of insulation, you’ll come across the term ‘thermal conductivity’, also known as a k-value or λ-value (lambda). This is the rate at which heat flows through a particular material, and good insulation will have a low thermal conductivity. It is measured in watts (heat flow) per metre (depth of material) per degree difference (inside to outside), so the unit is W/mK.
Most natural insulation materials (hemp, wool, recycled paper or textile) will have a thermal conductivity of about 0.035 to 0.040 W/mK, which is similar to the performance of conventional mineral wool insulation. Foil-backed plastic foam insulation boards are slightly better, with thermal conductivity about 0.023 W/mK. So about 100mm of the plastic foam board will give equivalent insulation value to about 150mm of the various woolly types.
Related Pages
Related events
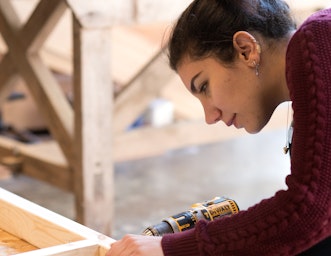

Zero Carbon Britain: Carbon Literacy for Communities Online
17th June 2025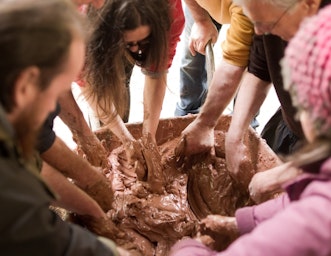
Cob Building
21st June 2025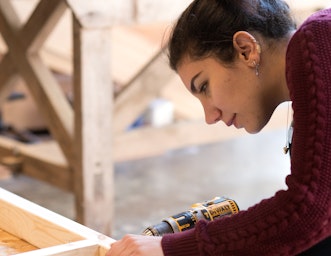
Build a Tiny House
4th July 2025Study at CAT: Our Postgraduate Courses
Related news
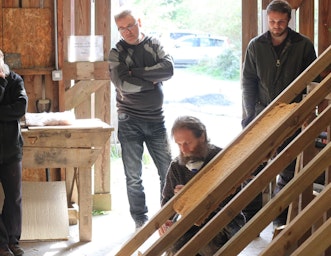
CAT stories – Nick Parsons and Mike Russell
29th January 2025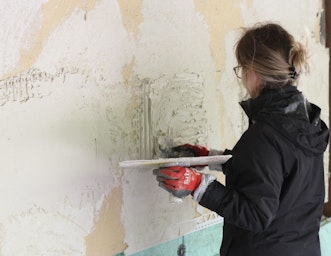
Ready for retrofit
29th January 2025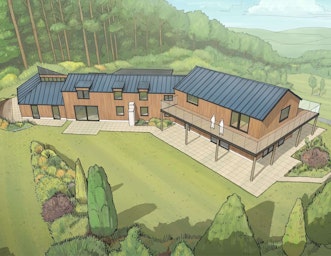
Hawkland — eco business takes flight
29th January 2025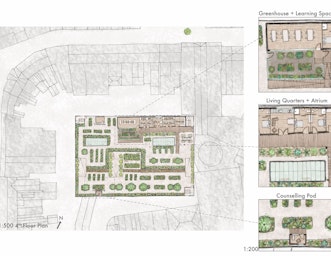
Designs for Life
23rd May 2024WANT TO LEARN MORE?
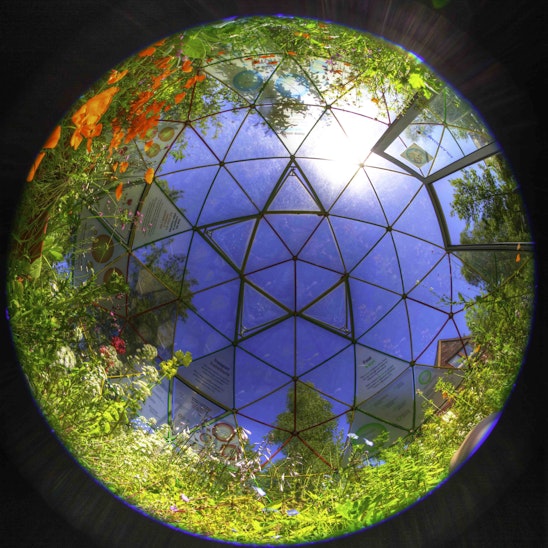
Did you know we are a Charity?
If you have found our Free Information Service useful, why not read more about ways you can support CAT, or make a donation.
Email Sign Up
Keep up to date with all the latest activities, events and online resources by signing up to our emails and following us on social media. And if you'd like to get involved and support our work, we'd love to welcome you as a CAT member.